استخراج سنگ آهن از ابعاد مختلف نقش مهمی در اقتصاد و تولید دارد. این تاثیر مستقیم و غیر مستقیم خودش را در چرخههای مختلف ایجاد ارزش نشان میدهد.
آهن جزء ضروری در تولید فولاد است. یعنی ماده اولیه ساخت و ساز، صنایع و هر بخشی از صنعت که فکرش را بکنیم. در این مقاله نگاهی خواهیم انداخت به مزیتهای بهرهبرداری از سنگ آهن، پروسه استخراج و انواع آن.
مراحل استخراج سنگ آهن
استخراج سنگ آهن به صورت عمومی از چند مرحله تشکیل میشود که عبارتند از:
کاوش: در این مرحله، محققان بر روی کانسارهای سنگ آهن با توجه به اطلاعات جغرافیایی و زمینشناسی، ابتدا به دنبال کشف و شناسایی معادن سنگ آهن میگردند.
حفاری: در این مرحله، با استفاده از دستگاههای حفاری، ژئوفیزیک و ژئوشیمیایی، سنگ آهن از سطح زمین حفر و استخراج میشود.
حمل و نقل: پس از استخراج سنگ آهن، آن را به کارخانه یا کارگاهی که برای فرآوری آن آماده است، منتقل میکنند.
خردایش: در این مرحله، سنگ آهن به قطعات کوچکتر خرد شده و به اندازهی مناسب برای فرآوری آماده میشود.
غربالگری: پس از خردایش، سنگ آهن را از آلودگیها و سنگهای بی ارزش دیگر جدا میکنند.
فرآوری: در این مرحله، سنگ آهن فرآوری و به صورت پودری یا پلتهایی که برای استفاده در فولادسازی مناسب هستند، تولید میشود.
ذخیرهسازی: پس از فرآوری، سنگ آهن آمادهی استفاده است و در انبارهای مختلف ذخیره میشود تا به صورت پودری یا پلتهایی که برای استفاده در فولادسازی مناسب هستند، به مشتریان ارسال شود
۵ مزیت استخراج سنگ آهن
۱. تجدید پذیری
یکی از مزیتهای مهم سنگ آهن این است که یک منبع تجدید پذیر است، به این معنی که پس از استخراج در طی زمان میتواند دوباره تجدید شود.
۲. امکان استخراج بدون حفاری عمیق
سنگ آهن را میشود از سطح زمین بدون نیاز به حفاری بیش از حد عمیق، یا استفاده بیش از حد انرژی استخراج کرد. این امر استخراج سنگ آهن را نسبت به سایر مواد معدنی یا فلزاتی که ممکن است به عملیات معدنکاری گسترده یا مقادیر زیادی انرژی برای استخراج نیاز داشته باشد، بسیار آسانتر میکند.
۳. سرعت استخراج
علاوه بر این، از آنجایی که میتوان استخراج سنگ آهن را نسبتا سریع انجام داد، این امر هزینه شرکتهایی که به سنگ آهن به عنوان ماده اولیه نیاز دارند کم میکند.
۴. موارد استفاده گسترده
مزیت دیگر سنگ آهن این است که می توان از آن در چندین محصول و فرآیند مختلف استفاده کرد. سنگ آهن جزء ضروری در تولید فولاد است و فولاد تبدیل به محصولات بسیار گسترده میشود.
به عنوان مثال، سنگ آهن را می توان در قطعات خودرو، خطوط راه آهن، مصالح ساختمانی برای پروژههای ساختمانی، ابزارهایی برای مقاصد تولیدی و حتی تجهیزات پزشکی استفاده کرد. این تطبیقپذیری به این معنی است که شرکتها هنگام تصمیم گیری در مورد نحوه استفاده از این منبع معدنی گزینههای بیشتری دارند.
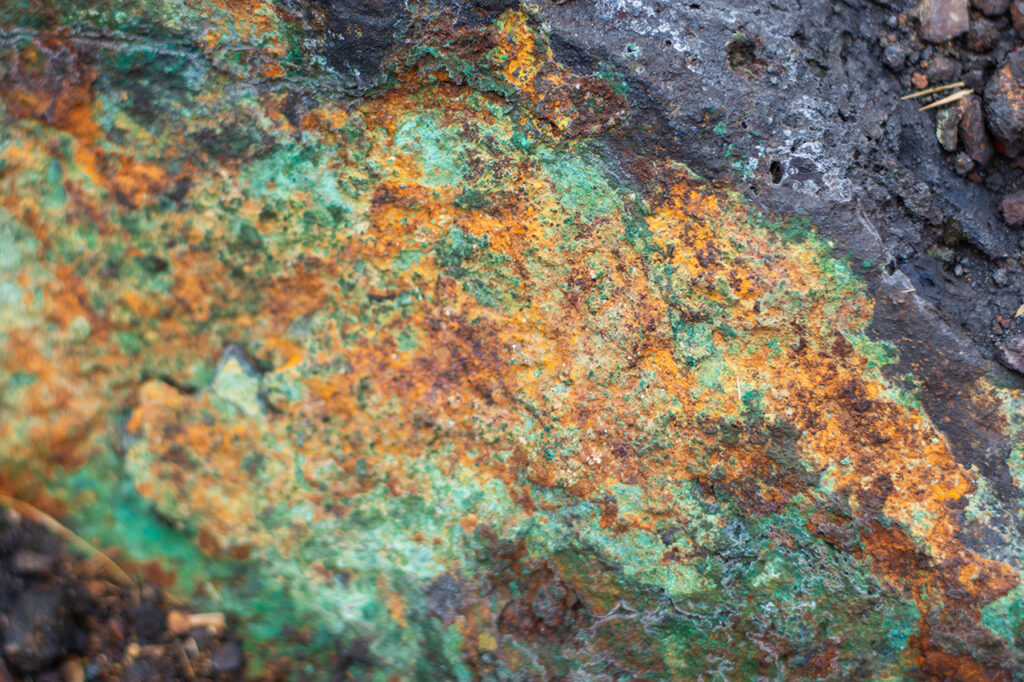
به طور خلاصه مهمترین ویژگیهای سنگ آهن که آن را با سایر مواد معدنی متفاوت میکند موارد زیر هستند:
- فراوانی سنگ آهن روی زمین نسبت به خیلی از انواع دیگر مواد معدنی زیاد است.
- سنگ آهن مادهای جامد و بادوام است که کاربردهای وسیعی دارد.
- استخراج و فرآوری سنگ آهن نسبتاً آسان است و آن را به گزینهای عالی برای ساخت و ساز و سایر کاربردها تبدیل میکند.
- تراکم بالای ماده خام آهن در سنگ آهن، آن را به یک ماده ایدهآل برای استفاده در تولید فولاد تبدیل می کند.
- سنگ آهن همچنین یک انتخاب محبوب برای استفاده در جواهرات و سایر اقلام تزئینی است.
روشهای استخراج
استخراج سنگ آهن یک فرایند قدیمی است که از هزاران سال پیش در سراسر جهان انجام میشد.اما به مرور روشهای آن پیشرفتهتر شد و از تکنولوژیهای جدید برای آن استفاده شد. این روشها شامل استخراج باز و بسته و استخراج از برف و یخ میشوند.
در روش استخراج باز، معدنهای سنگ آهن از زیر زمین خارج میشوند. این روش شامل حفاری، انفجار و حمل و نقل مواد استخراج میشود.
در روش استخراج بسته، سنگ آهن را سطح زمین خارج میکنند. این روش شامل معدنهای رودخانهای، کارخانههای شن و ماسه، معدنهای روباز و معادن زیرزمینی است.
کاربردهای سنگ آهن
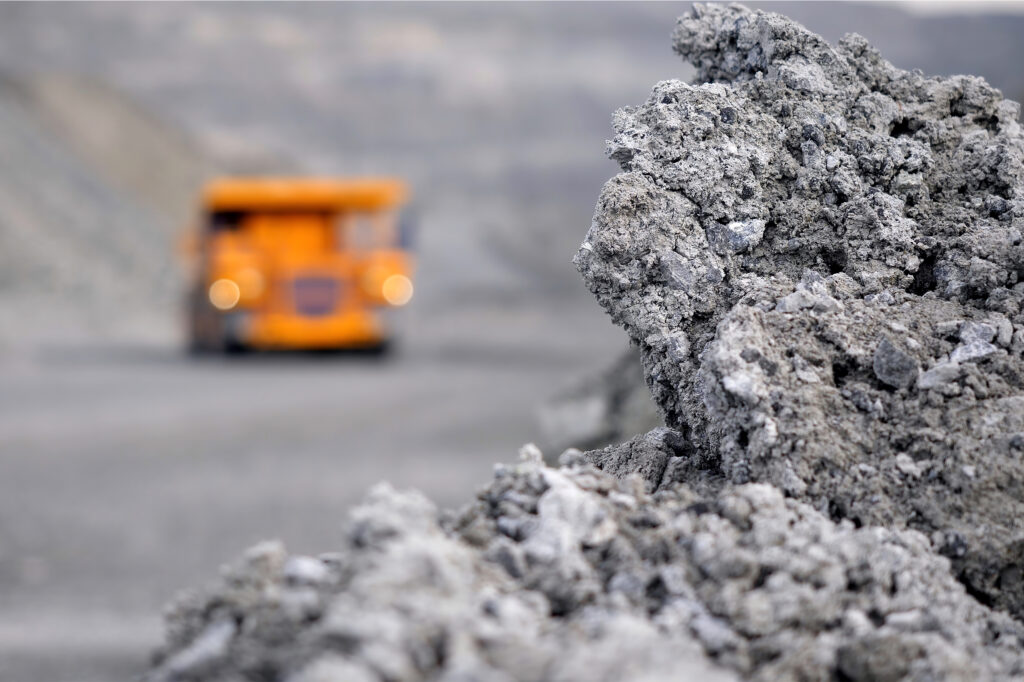
سنگ آهن به عنوان یکی از مهمترین مواد اولیه در تولید فولاد و دیگر فلزات استفاده میشود. همانطور که اشاره شد، فولاد یکی از مهمترین فلزات در بسیاری از صنایع است و برای ساخت قطعات خودرو، ساخت ساختمانها، ساخت ماشینآلات و ابزارهای صنعتی، ساخت اسباب بازی، ساخت لوازم خانگی و بسیاری دیگر از مصارف استفاده میشود.
در بسیاری از کشورها، سنگ آهن یکی از مهمترین منابع درآمدی است. سنگ آهن در کنار طلا و مس از ارزشمندترین مواد معدنی محسوب میشود.
چه میزان از سنگ آهن جهت تولید فولاد استفاده میشود؟
میزان استفاده از سنگ آهن برای تولید فولاد به عوامل مختلفی مانند نوع سنگ آهن، فرآیند تولید فولاد، فناوریهای مورد استفاده و … بستگی دارد. اما به طور کلی، برای تولید یک تن فولاد حدود ۱.۶ تا ۲.۲ تن سنگ آهن به صورت سنگ خام (بدون فرآوری) نیاز است. اما با فرآوری سنگ آهن و جداسازی مواد آهنی از مواد غیرآهنی، میتوان از سنگ آهن استخراج شده، مقدار بیشتری آهن را به دست آورد که برای تولید فولاد مورد استفاده قرار میگیرد.
در طول روند تولید فولاد، از مواد دیگری نیز مانند کک، ذوب شده فلزی، آهن اسفنجی و … استفاده میشود که به دلیل نوع فرآیند تولید و نیز اهداف مختلف تولید در هر کارخانه متفاوت است.
میزان استخراج سنگ آهن در سراسر دنیا
سازمان جهانی معادن میگوید، در سال ۲۰۲۰، بیش از ۲.۴ میلیارد تن سنگ آهن در سراسر جهان استخراج شده است. برزیل، استرالیا، هند، روسیه، چین، آمریکا، کانادا، آفریقای جنوبی و اوکراین از جمله کشورهایی هستند که بیشترین مقدار سنگ آهن را استخراج میکنند.
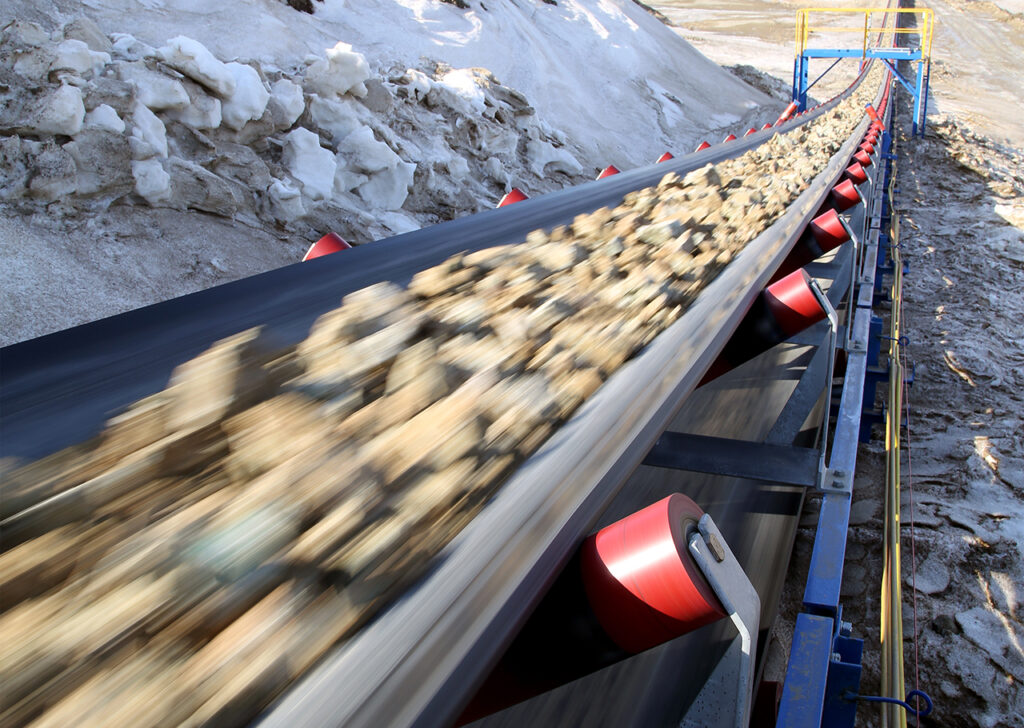
فرآوری سنگ آهن به عنوان یکی از صنایع مهم در سراسر دنیا، دارای تأثیر بسیاری بر روی اقتصاد جهانی است. براساس آمارهای ارائه شده توسط سازمان جهانی معادن، بیشترین مقدار سنگ آهن در سال ۲۰۲۰ به ترتیب در برزیل، استرالیا و هند استخراج شده است.
به عنوان مثال، برزیل که یکی از بزرگترین تولیدکنندگان سنگ آهن جهان است، در سال ۲۰۲۰ بیش از ۳۷۰ میلیون تن سنگ آهن را استخراج کرده است. این صنعت در برزیل به عنوان یکی از مهمترین منابع درآمدی شناخته شده است. این صنعت باعث اشتغال بسیاری از جمعیت برزیل شده است و به منظور افزایش صادرات، دولت برزیل سیاستهایی را برای توسعه این صنعت اجرا کرده است.
- برزیل با استخراج ۳۷۰ میلیون تن در سال ۲۰۲۰، بیشترین مقدار را داشته است.
- استرالیا با استخراج ۹۰۰ میلیون تن در سال۲۰۲۰، دومین کشور است.
- هند با استخراج ۲۱۰ میلیون تن در سال ۲۰۲۰، سومین کشور است.
چالشهای استخراج سنگ آهن
این صنعت به عنوان یکی از صنایع معدنی پیچیده و زمانبر شناخته میشود. در ادامه به چند دلیل آن اشاره میکنیم.
۱. افزایش هزینهها
یکی از چالشهای اساسی، افزایش هزینهها است. هزینههای این کار در سالهای اخیر به دلیل افزایش هزینههای حمل و نقل، افزایش قیمتهای انرژی و کاهش غنیسازی مواد معدنی افزایش یافته است.
۲. کمبود منابع آب
خارج کردن سنگ آهن از پوسته زمین نیاز به منابع آب دارد، با این وجود در بسیاری از مناطق جهان کمبود منابع آب وجود دارد که این مسئله میتواند به چالش برانگیزد.
۳. محیط زیست و اثرات آن
استفاده از تکنولوژیهای پایدار و محیط زیستی، استفاده از روشهای بهداشتی در استخراج، کاهش مصرف انرژی و آب، بازیافت کردن مواد معدنی و مدیریت پسماندها در پروسه استخراج بسیار مهم است. البته مدیریت پایدار نه فقط در بخش استخراج بلکه در تمام حلقههای زنجیره تولید فولاد مهم و حیاتی است.
۴. کاهش کیفیت مواد معدنی
با گذر زمان، کیفیت سنگ آهن کاهش مییابد. یعنی سرعت فرآوری سنگ آهن خیلی مهم است. این مسئله میتواند به کاهش بازدهی و افزایش هزینهها منجر شود.
هر نوع سنگ آهن دارای خصوصیاتی منحصر به فرد است که آن را از دیگر نوعها متمایز میکند. در ادامه، برخی از انواع سنگ آهن را با جزئیات بیشتری بررسی میکنیم.
انواع سنگ آهن
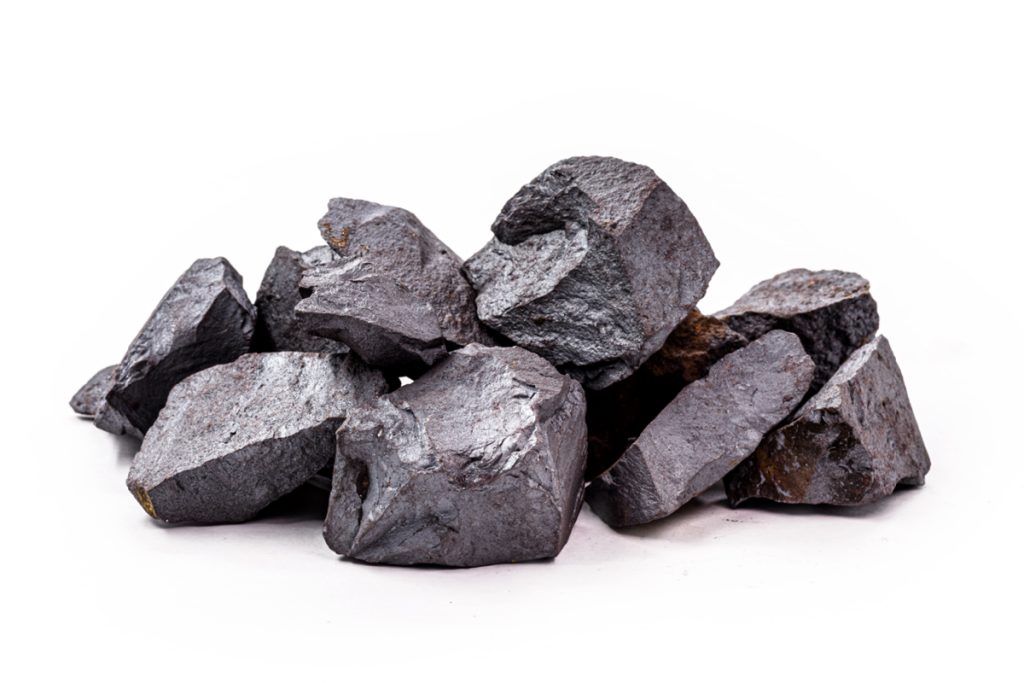
هر نوع سنگ آهن دارای خصوصیاتی منحصر به فرد است که آن را از دیگر نوعها متمایز میکند. در ادامه، برخی از انواع سنگ آهن را با جزئیات بیشتری بررسی خواهیم کرد:
مگنتیت
مگنتیت یکی از انواع سنگ آهن است که دارای تراکم بالایی از آهن است و در حالت طبیعی به صورت مغناطیسی است. این نوع سنگ آهن در بسیاری از مناطق جهان مانند استرالیا، برزیل، آمریکا و… استخراج میشود. مگنتیت به دلیل محتوای بالای آهن، در صنایع فولادسازی، ساخت مواد ضد زنگ و… استفاده میشود.
هماتیت
هماتیت دارای رنگ خاکستری تا سرخ روشن است و به صورت اکسید آهن در طبیعت یافت میشود. این نوع سنگ آهن در بسیاری از مناطق دنیا مانند هند، استرالیا، روسیه و … استخراج میشود. هماتیت به دلیل محتوای بالای آهن، در صنایع ساخت قطعات خودرو، ساخت ابزارهای برقی و… استفاده میشود.
سیدریت
سیدریت یکی از انواع سنگ آهن است که دارای رنگ خاکستری تا قهوهای است و به صورت کربنات آهن در طبیعت یافت میشود. این نوع سنگ آهن در بسیاری از مناطق جهان مانند ایران، آلمان، ایتالیا و… استخراج میشود. سیدریت به دلیل محتوای بالای آهن و خواص آن، در صنایع تولید فولاد، ساخت قطعات خودرو و… استفاده میشود.
لیمونیت
لیمونیت یکی از انواع سنگ آهن است که دارای رنگ سیاه است و معمولا به صورت هیدرات آهن در طبیعت یافت میشود. این نوع سنگ آهن در بسیاری از مناطق دنیا مانند استرالیا، روسیه، آمریکا و… استخراج میشود. لیمونیت به دلیل محتوای بالای آهن و خواص آن، در صنایع تولید فولاد، ساخت قطعات خودرو و… استفاده میشود.
کنگرلومریت
کنگرلومریت یکی از انواع سنگ آهن است که دارای رنگ خاکستری تا مشکی است و به صورت آهن اسفنجی در طبیعت یافت میشود. این نوع سنگ آهن در بسیاری از مناطق دنیا مانند آفریقای جنوبی، استرالیا و… استخراج میشود. کنگرلومریت به دلیل محتوای بالای آهن و خواص آن، در صنایع فولادسازی، ساخت قطعات خودرو و… استفاده میشود.
تیتانوم مگنتیت
تیتانوم مگنتیت حاومی مقدار بالایی از آهن و تیتانیوم است. این نوع سنگ آهن در برخی مناطق جهان مانند استرالیا، کانادا و… استخراج میشود. تیتانوم مگنتیت به دلیل محتوای بالای آهن و تیتانیوم، در صنایع هوافضا، صنایع الکترونیکی و… استفاده میشود.
مراحل فرآوری سنگ آهن
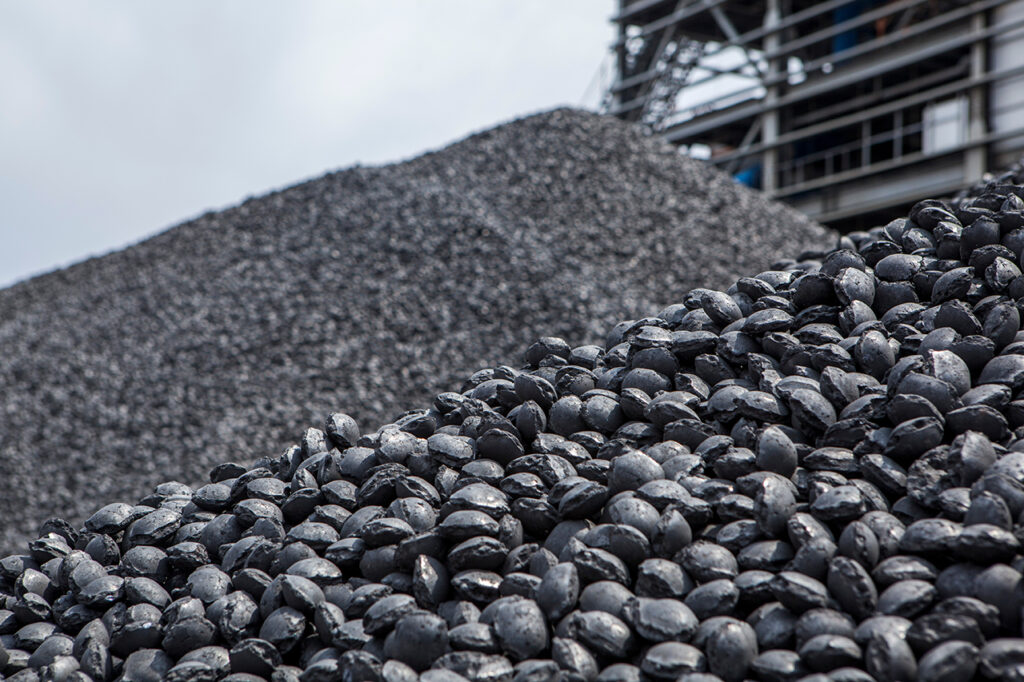
سنگ آهن به عنوان یکی از مهمترین مواد اولیه در صنایع فولادسازی و فلزیابی، از طریق چندین فرآیند فرآوری میشود. در ادامه، به برخی از مراحل فرآوری سنگ آهن اشاره میکنیم:
خرد کردن: ابتدا سنگ آهن با استفاده از دستگاههای خردکن، به قطعات کوچکتر خرد میشود تا به راحتی قابل فرآوری باشد.
غربالگری: پس از خرد کردن، سنگ آهن را از آلودگیها و سنگهای بی ارزش دیگر جدا میکنند. برای این کار از دستگاههای غربال استفاده میشود.
آسیاب کردن: در این مرحله، قطعات سنگ آهن را به صورت پودری خرد میکنند. این پودر سپس به دستگاههای مختلفی ارسال میشود.
مغناطیسی کردن: برای جداسازی مواد آهنی از مواد غیرآهنی، از دستگاههای مغناطیسی استفاده میشود. در این دستگاهها، یک میدان مغناطیسی قوی ایجاد میشود که باعث جداسازی ماده آهنی از مواد غیرآهنی میشود.
فلوتاسیون: در این روش، با استفاده از دستگاههای خاص، سطح آب را به طور کنترل شده افزایش میدهند تا مواد فلزی و غیرفلزی با چگالی متفاوت، از هم جدا شوند.
خشک کردن: پس از انجام فرآیندهای فوق، ماده آهنی به صورت ترکیبی با آب است. برای جداسازی آب از ماده آهنی، از دستگاههای خشک کن استفاده میشود.
سربارهزدایی: در این مرحله، سربارههای تولید شده در فرآیند فرآوری را از ماده آهنی جدا کرده و آن را از دستگاههای خاصی عبور میدهند.
برای آشنایی بیشتر با مراحل فرآوری سنگ آهن، این مقاله را بخوانید.
برای نوشتن این مقاله از منابع زیر بهره بردهایم: